Solving Typical Automated Feeder Challenges
When it comes to maintaining a smooth operation in automated feeding systems, the devil is often in the details. A loose screw can bring a production line to a standstill, turning a once reliable machine into a source of downtime and frustration. In the realm of backyard wildlife, a squirrel outsmarting a bird feeder can be as disconcerting as a machinery malfunction for a keen observer. Mastering the art of troubleshooting is akin to crafting a persuasive advertising campaign: it requires insight, patience, and a strategic approach. In this article, readers will discover effective solutions for overcoming common automated feeder challenges and ensuring seamless functionality.
Identifying Common Automated Feeder Problems
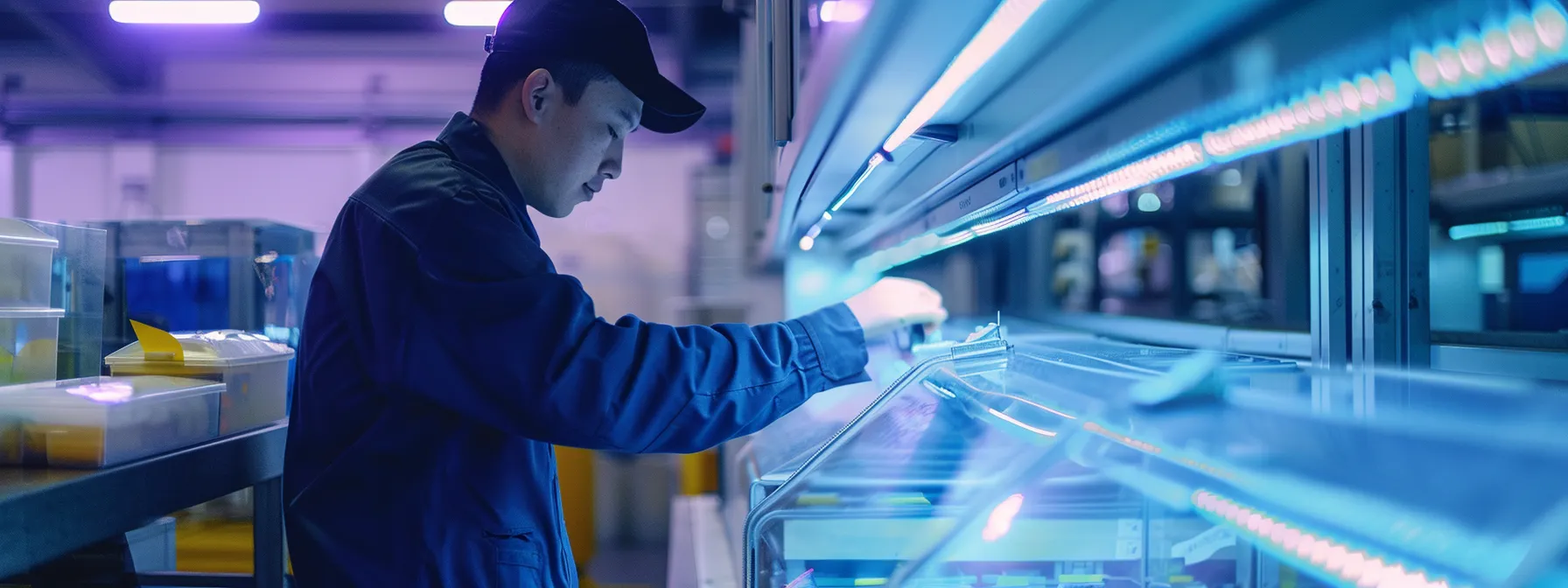
In the complex ecosystem of automated feeders, vigilance in spotting early problems can protect both the health of the machinery and the smooth operation of the manufacturing process. With water potentially corroding sensitive components, a stray wire causing unexpected malfunctions, or a misaligned sensor disrupting the flow, identifying feeder issues swiftly is key. Recognizing symptoms of feeder malfunctions demands a keen eye for detail and an understanding of each part’s function. Professionals must discern the subtleties between mechanical wear and electrical failure, and evaluate how these faults could throttle the productivity of the entire production line. Addressing these challenges not only prevents extended downtime but also safeguards the quality of the output, maintaining the integrity of the manufacturing system.
Recognizing Symptoms of Feeder Malfunctions
Manufacturers often detect a malfunction in automated feeders by observing irregularities in the handling of materials like metal, which should flow consistently. A sudden jolt or halt in the system could indicate undue pressure or abrasion within the mechanism, which, if left unchecked, might escalate to more severe damage or a complete breakdown of operations.
Similarly, disruptions in feed consistency, akin to the unpredictable flight pattern of a bird, may be symptomatic of underlying imbalances. Variations in weight distribution or inconsistencies molded into the materials being processed can cause unforeseen strain on the feeder’s components, necessitating thorough inspection and calibration to avert operational deficiencies.
Differentiating Between Mechanical and Electrical Issues
Distinguishing between mechanical issues and electrical problems within an automated feeder requires a precise understanding of the machine‘s operation. Mechanical faults often manifest as aberrant wear on moving parts or irregular discharge patterns, indicating that components may need realignment or replacement to restore proper volume throughput.
On the contrary, electrical issues tend to present subtler symptoms, such as the feeder’s failure to initiate or inconsistencies in pneumatic controls. Technicians must swiftly address these anomalies to prevent stalling or erratic machine behavior that could compromise the precision of operations.
Assessing the Impact on Production Line Efficiency
Fluctuations in an automated feeder’s performance directly influence the efficiency of a production line, affecting the timely delivery of nutrition elements crucial in sectors such as farm production. When feeders process materials like plastic with precision, the pace of manufacturing maintains its predictability, thereby optimizing the whole system’s throughput and accuracy.
In environments where automation is a core component of operations, inconsistencies in feeder behavior act as bottlenecks, reducing the rhythm of production and potentially compromising both the quantity and quality of the end product. Prompt resolution of such feeder issues ensures continuous flow and sustains the industry’s overarching goal of seamless, efficient production.
Recognizing the issues with automated feeders is just the beginning. Now, let’s tackle the practical side and guide you through the troubleshooting process.
Steps for Troubleshooting Automated Feeders
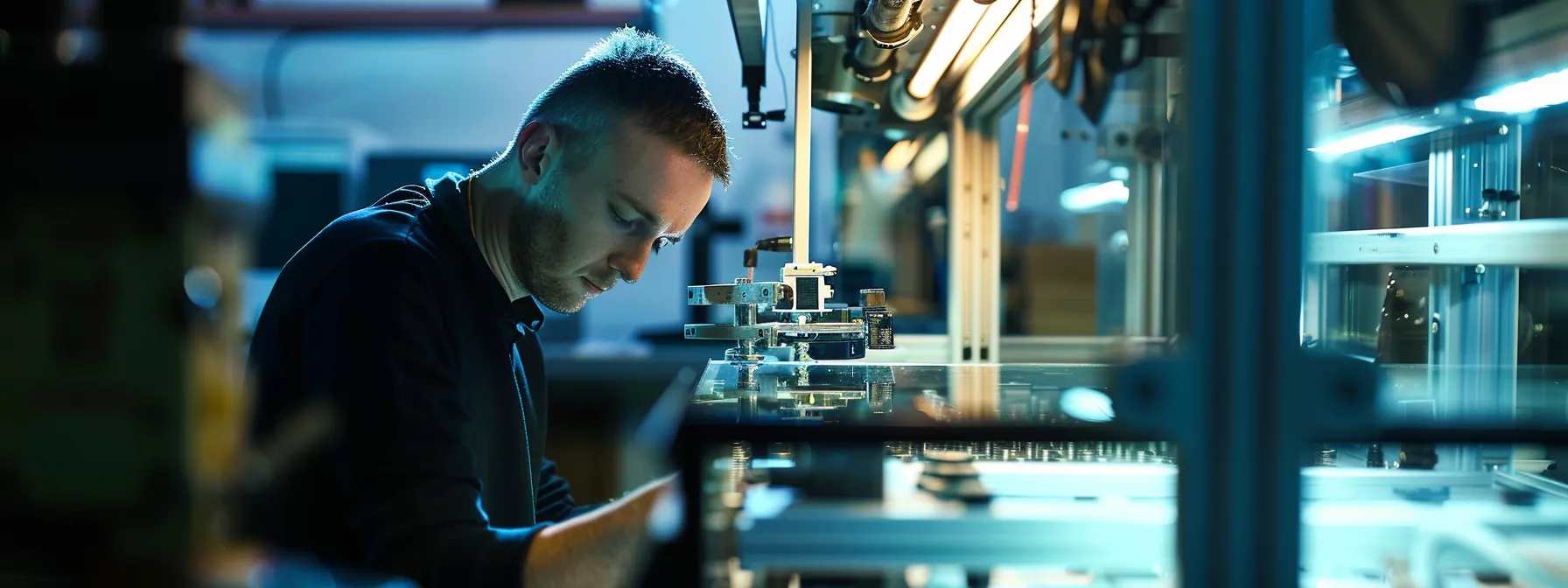
Approaching automated feeder challenges requires a systematic strategy, grounded in technical awareness and a proactive stance against inefficiency. Initial diagnostics serve as the cornerstone for pinpointing disruptions within the feeder’s complex mechanisms. Technicians evaluate power supply and control settings, ensuring that voltage irregularities or misconfigured parameters are not impeding the desired speed and precision of the machine. In welding applications where precision feeds of powder are crucial, even slight deviations can lead to considerable waste. A thorough check for mechanical wear, obstructions, and the health of pivotal components is essential to restore the feeder’s integrity. Confirming the proper operation of sensors and actuators is critical, as the equipment relies on these devices for seamless function. When knowledgeable technicians assess and address each of these elements, the road to optimal performance and the elimination of operational hurdles becomes clear.
Conducting Initial Diagnostics to Pinpoint Issues
When addressing automated feeder challenges, initiating a series of diagnostic checks is a critical first move towards maintaining productivity. Technicians begin by scrutinizing the power supply, ensuring the voltage levels are stable, as fluctuations can severely impact the feed mechanisms and lead to costly downtime.
Assessment of the equipment’s wear and tear is also imperative; this includes checking for any signs of deterioration that could impede the feeder’s function. Identifying these issues early helps to minimize further damage and maintain the smooth functioning of the manufacturing process:
- Examine the stability and consistency of the power supply to the automated feeder.
- Inspect the feeder for any signs of wear and tear that could affect performance.
Checking Power Supply and Control Settings
An integral aspect of troubleshooting automated feeders involves scrutinizing the power supply to identify issues that could be causing malfunctions. Irregularities in voltage or frequency can wreak havoc on the operation of these machines, especially in environments like agriculture where consistent performance is critical to manage large-scale production.
After verifying that power levels are stable, technicians then adjust control settings to rectify any deviations in the feeder’s behavior. The presence of dust, common within the agricultural sector, or misalignment of components like the engine could alter feed flow and hinder the effectiveness of operations.
Checklist Item | Description | Status |
---|---|---|
Voltage Stability | Ensure the feeder receives a consistent voltage level. | To be checked |
Frequency Regulation | Check if the frequency of the power supply is within acceptable range. | To be checked |
Dust Accumulation | Inspect for dust build-up that may affect feeder sensors and controls. | To be checked |
Control Settings | Review and adjust control parameters to ensure optimal operation. | To be checked |
Engine Performance | Examine the engine and related mechanisms for signs of wear or misalignment. | To be checked |
Inspecting for Mechanical Obstructions or Wear and Tear
Meticulous examination for mechanical obstructions stands as a pillar of proactive maintenance. Technicians diligent in their inspection can avert complications by ensuring that pathways for extrusion are clear from any materials that could introduce blockages or inefficiencies.
Use of a suitable lubricant plays a central role in preventing wear and tear; it keeps moving parts functioning smoothly, thus upholding the feeder’s longevity and efficiency. Regular checks for moisture intrusion are equally important, as this can degrade lubricants and lead to rust, compromising the structural integrity of feeder components.
- Perform thorough inspections to identify and clear any mechanical blockages.
- Administer lubricant to mechanical parts to ensure smooth operation and reduce wear.
- Check for moisture presence that might compromise lubrication and lead to corrosion.
Testing Sensors and Actuators for Proper Operation
Ensuring the reliability of sensors and actuators within automated feeders is as crucial as a steady heartbeat is to an animal. Technicians test these components to prevent system failures that could mirror the effects of a disease, impeding operation. By verifying sensor accuracy and actuator response, they ensure feed pumps function without the hindrance of rust or debris.
Accurate sensors act as the eyes of the feeder system, detecting any anomalies, while actuators — the hands — respond aptly to the commands given. It’s vital to ascertain that these elements are free from defects and contamination as even a small amount of rust or debris can compromise the precise actions required in a high-stakes production environment.
As we navigate the intricacies of automated feeder maintenance, an unexpected twist can often arise: mechanical failures. Let’s tackle these head-on, ensuring your automated feeder continues to perform at its peak.
Addressing Mechanical Failures in Automated Feeders
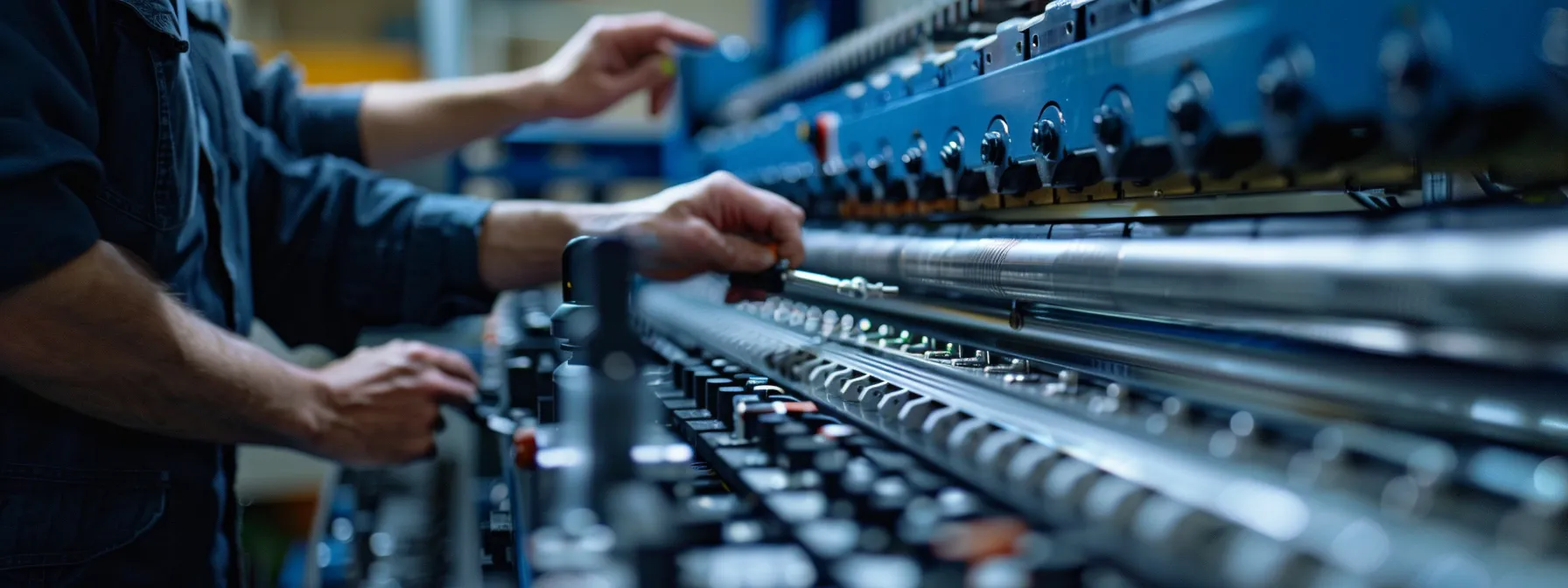
In the realm of automated feeders, addressing mechanical failures is a critical task that demands precise, timely interventions. The strength and durability of these systems are often subjected to considerable stress, leading to the gradual wear or abrupt damage of vital components. Professionals approach these situations with expert calibration techniques, ensuring each element is finely tuned for peak performance. Replacing worn or damaged parts is a necessary response to the unyielding forces, like wind and the constant flow of liquid or other materials that an automated feeder must manage. Similarly, proper feeder alignment and tension adjustments are paramount for maintaining the harmonious operation of the machinery’s intricate instrumentation. Furthermore, the regular lubrication of moving parts is an essential maintenance practice, thwarting the harsh friction that can otherwise disrupt a feeder’s smooth operation. Attention to these aspects preserves the feeder’s integrity, underpinning the success of automated processes across various industries.
Replacing Worn or Damaged Components
Replacing worn or damaged components in automated feeders is a proactive step to prevent the hazards that can arise from compromised machinery. Technicians conduct a meticulous inspection of the feeder, with a particular focus on the hopper, where seeds are stored, ensuring that any faltering part that could alter the density and flow of the seeds is promptly identified and substituted.
An integral part of feeder maintenance is identifying parts that are nearing the end of their useful life before they break down and become a hazard. This is often achieved through regular inspections, with special attention to the hopper’s integrity and the smoothness of seed flow, safeguarding against irregular density that can lead to operational inefficiencies.
Adjusting Feeder Alignment and Tension
In the realm of resolving mechanical failures in automated feeders, precise alignment and correct tension are vital. The continuous exposure to humidity may lead to expansion or contraction of feeder pipes, necessitating adjustments to maintain optimal flow through the valve systems. Technicians must assess the expansion coefficients of materials used and apply this knowledge to ensure that technology-driven feed mechanisms operate flawlessly, regardless of environmental changes.
Furthermore, the application of an appropriate coating to feeder components can greatly reduce the effects of wear and enhance the technology‘s robustness. Regularly checking and adjusting the tension in the system’s belts or chains is integral to prevent slippage due to variable pipe diameter. Such maintenance ensures that valves open and close with precision, a testament to the meticulous attention paid to the operational harmony of automated feed systems.
Lubricating Moving Parts to Ensure Smooth Operation
Ensuring that all moving components of automated feeders are sufficiently lubricated is fundamental to maintaining machine efficiency. Lack of proper lubrication can cause increased friction and wear, hindering the feeder’s reliability and potentially violating the privacy policy of the processing plant by causing unintended disruptions.
Technological innovation in the lubrication materials, methods, and systems has made it possible to extend the life of machine parts, contributing to sustainability and reducing the need for frequent recycling of components. An added benefit of using advanced lubricants is that they create less residue on paper products being processed, which aligns with the emphasis on privacy in product handling.
Maintenance Task | Action | Benefit |
---|---|---|
Lubrication of moving parts | Apply advanced lubricants to reduce friction | Enhanced machine reliability and longevity |
Compliance with privacy policy | Ensure lubrication process does not cause product compromise | Maintain integrity and privacy of processed items |
Innovation in lubrication | Employ cutting-edge lubrication technologies | Reduced maintenance frequency and component recycling |
Residue reduction on paper products | Select lubricants with minimal processing impact | Consistent product quality and privacy assurance |
Troubleshooting mechanical failures is only half the battle. Next, we tackle the electrical issues that keep automated feeders running smoothly.
Solving Electrical Issues in Automated Feeding Systems
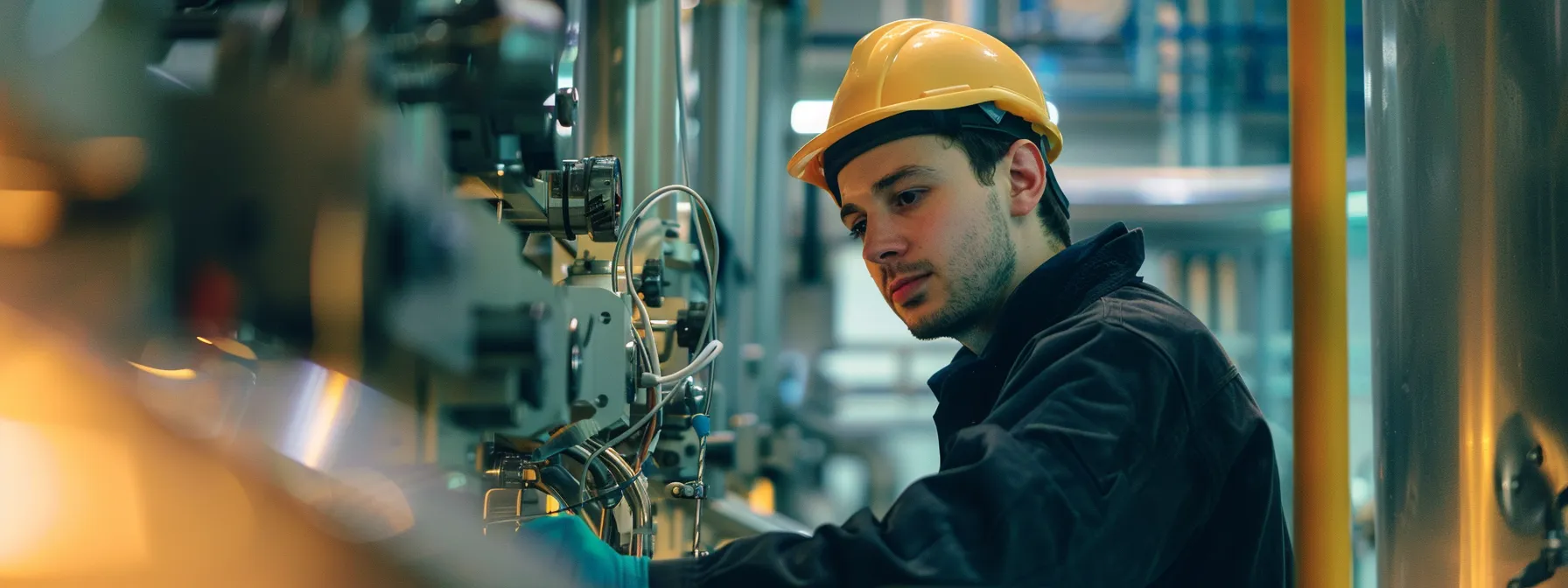
In automated feeding systems that are essential to the streamline operations of industries such as dairy production, electrical issues can be both subtle and pervasive. This segment delves into crucial troubleshooting solutions for addressing and mitigating electrical challenges that may arise. When integral components like vacuum conveyors and precise measurement sensors succumb to problems stemming from loose wiring or system contamination, the repercussions on a plant‘s productivity can be significant. Technicians must tackle these problems directly—securing connections, refreshing feeder software, and swapping out malfunctioning sensors and actuators. Implementing these solutions not only revitalizes the equipment’s efficiency but also ensures the dairy plant maintains its strict standards for hygiene and product quality.
Securing Loose Wiring and Connections
In tackling the root causes of malfunctions in automated feeder systems, attention to the security of wiring connections is crucial. Technicians carefully scrutinize the apparatus to confirm all electric pathways remain intact, ensuring that the motor drive receives a consistent influx of electricity without interruption. This step is vital in following a maintenance policy that precludes erratic machine performance.
A loose connection can drastically impact the ratio of input to output power in feeder systems, leading to unplanned halts in operation. By methodically securing each wiring interface, technicians safeguard the transmission of electricity, upholding the motor drive‘s capacity to perform efficiently and in accordance with established operating standards.
Updating or Resetting Feeder Software
In the realm of automated feeding systems, the refreshment or upgrading of feeder software plays an integral part in curbing the pernicious effects of corrosion on electrical components. Frequently, issues like a compromised relay function or a faulty shopping cart mechanism in the system can be resolved by updating the software to ensure clear communication signals and consistent power delivery.
Addressing software glitches that cause miscommunication between sensors and relays is paramount to sustaining the feeder’s operational integrity. A well-executed reset or update can revitalize the software, enabling it to accurately interpret signals and manage power distribution without the interference that may lead to production inefficiencies.
Replacing Faulty Sensors and Actuators
In the intricate dance of automated feeding systems, the assurance of material flow hinges on the flawless operation of sensors and actuators. When these critical components falter, a domino effect jeopardizes the entire production cycle, necessitating immediate intervention. It falls to skilled technicians to identify and replace any units compromised by dust from raw materials, which can impair the delicate balance of pneumatic controls and disrupt the feeders’ precision.
During routine maintenance, an emphasis on cleaning and inspecting sensors and actuators ensures the longevity of the system and the integrity of the material handling process. A proactive replacement of these elements, particularly when they show signs of wear or damage, sustains unobstructed flow and circumvents costly production setbacks. :
- Swiftly replace sensors and actuators showing signs of malfunction to sustain material flow.
- Implement rigorous cleaning protocols to preserve pneumatic control efficiency.
- Conduct regular inspections to detect wear and preemptively replace components to ensure uninterrupted operation.
Resolving electrical malfunctions paves the way for enhanced functionality. Let’s shift our focus to optimizing feeder performance to ensure peak productivity.
Optimizing Feeder Performance After Troubleshooting
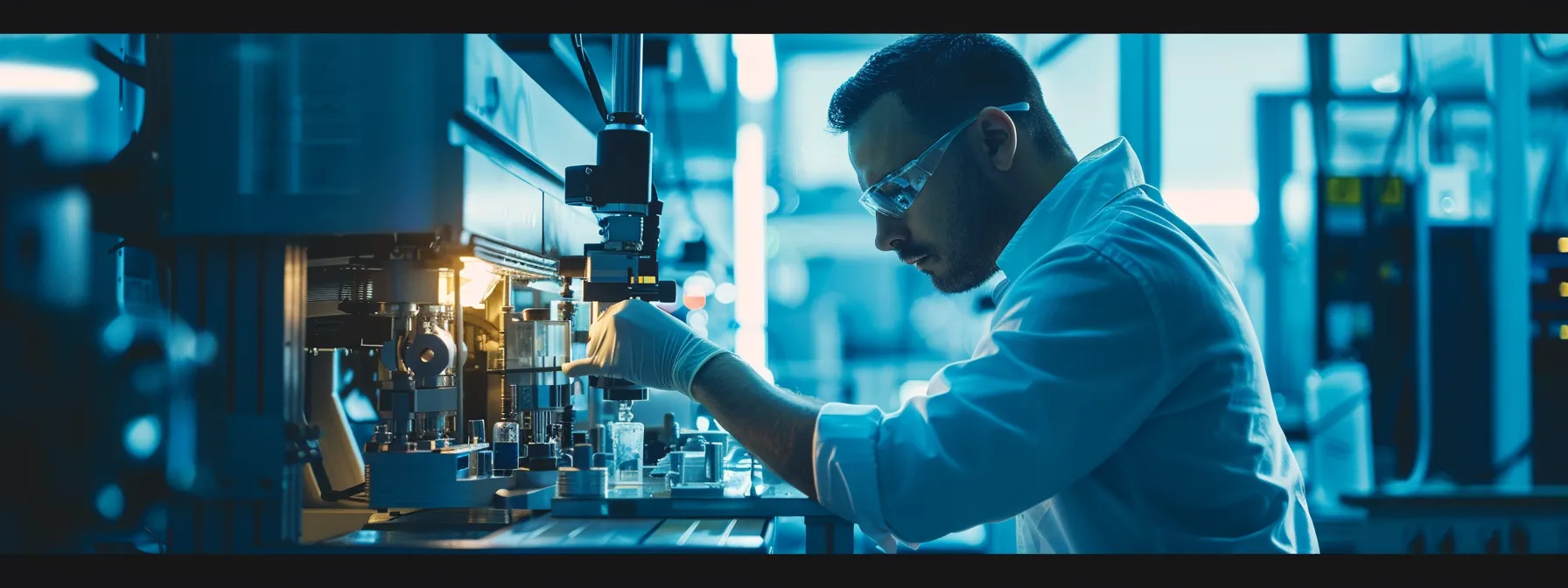
Once the immediate challenges posed by automated feeder malfunctions have been addressed, the focus shifts to enhancing the machinery’s operation for long-term efficacy. It is vital for professionals in contact with these systems to refine feed rates, ensuring that bulk materials transition smoothly through the feeder without causing obstructions or system overloads. Regular calibration emerges as a key practice to maintain the precision essential for consistent output while implementing preventive maintenance schedules mitigates the risk of future malfunctions. With a robust backup strategy in place, facilities can anticipate potential issues and swiftly switch to contingency plans, thereby maintaining uninterrupted production and preserving the feeder’s longevity.
Fine-Tuning Feed Rates for Optimal Material Flow
Adjusting the feed rates of automated feeders requires precision, akin to tuning a finely crafted stainless steel instrument. Technicians consider the unique properties of each material, using the information from prior diagnostics to set the flow that minimizes blockages and ensures a consistent output. This vital adjustment is often managed through sophisticated control systems operating on platforms like Microsoft Windows, delivering a level of refinement critical for seamless operations.
As professionals address the calibration of automated feeders, they often keep a detailed record of the adjustments made, which are easily documented and shared via email address contacts for future reference. Monitoring tools such as Task Manager on Microsoft Windows enable the overseeing of system performance in real time, ensuring the feeder operates within the optimal parameters, a task that underpins the efficiency and reliability of the entire material handling process.
Regular Calibration to Maintain Accuracy
Calibration is an intricate process that ensures feeder systems respond accurately to commands issued by computer hardware via a user interface. This procedure often involves connecting devices through a USB interface for direct communication with the operating system, enabling precise adjustments that align with the intricate demands of automated machinery.
Moreover, with advancements in internet technology, professionals can remotely monitor and calibrate feeder operations using secure HTTP protocols. Such remote servicing not only provides convenience but also ensures that feed rates and system accuracies are consistently optimized, providing increased reliability and performance.
Implementing Preventive Maintenance Schedules
Professionals are increasingly utilizing mobile apps to seamlessly initiate preventive maintenance schedules on automated feeders, ensuring that machines stay on the correct path to optimal performance. These applications, often accessed via a laptop or computer, provide real-time analytics and notifications, guiding maintenance teams in executing timely interventions before potential issues exacerbate.
Centralized server systems play a pivotal role in aggregating data from feeder operations across a facility, allowing predictive maintenance models to run sophisticated algorithms that determine maintenance needs. By leveraging this server-hosted information, facilities can prevent downtime, ensuring that automated feeders consistently meet production demands.
Once the feeder’s performance hiccups are ironed out, a fresh chapter begins. Professional expertise now steps into the spotlight, ready to tackle the most stubborn of feeder conundrums.
Leveraging Professional Support for Complex Feeder Problems
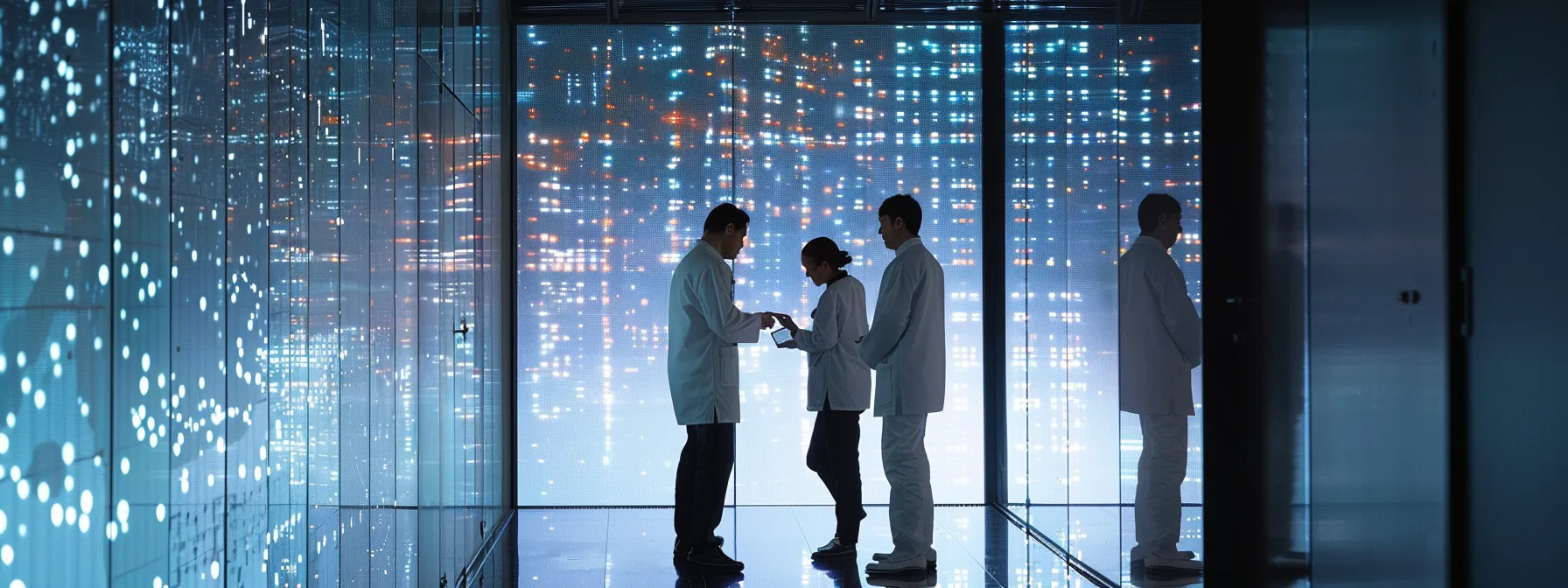
In the intricate dance of automated feeding system management, there comes a juncture where the in-house menu of solutions exhausts itself, dictating the need for expert intervention. Calling upon seasoned professionals with a robust toolset and up-to-date patches can swiftly transform an out-of-sorts feeder system back to its optimal state. Contracts that provide ongoing technical support offer a safety net, knitting a patchwork of preventive maintenance with seamless access to expert services. Moreover, equipping operational staff with training on basic maintenance and troubleshooting procedures enhances their ability to respond to data-driven messages from the system, fostering a proactive stance towards equipment care. By understanding these pivotal strategies, facilities can enhance the proficiency of their automated feeders, ensuring a consistent message of efficiency and reliability is maintained.
When to Call in Experts for Troubleshooting and Repairs
When systemic malfunctions persist despite rigorous on-site troubleshooting, it’s time to call in experts. These seasoned professionals bring a fresh perspective, with specialized diagnostic tools and software, to resolve complex issues that surpass the typical capabilities of in-house personnel.
By utilizing advanced troubleshooting software accessed via a web browser, experts can remotely identify and address the crux of feeder problems. Users may simply click an icon or button, providing these specialists with real-time data, streamlining the repair process and minimizing operational downtime.
Issue | User Action | Expert Solution |
---|---|---|
Persistent Systemic Malfunction | Engage expert troubleshooting support | Specialized tools and software diagnose and fix complex issues |
Remote Diagnostic Requirement | Use web browser to click support icon or button | Expert remote analysis and expedited repair process |
Benefits of Ongoing Technical Support Contracts
Engaging in ongoing technical support contracts furnishes companies with access to an extensive directory of expertise, tailored to mitigate issues with automated feeders. This kind of partnership ensures that experienced technicians are routinely overseeing the machinery’s operational health, proficiently handling complex scenarios from problematic device drivers to sleep mode errors.
Maintenance contracts frequently cover an array of technological contingencies, including updates to device drivers and resolving connectivity issues, such as those involving bluetooth. This preemptive support optimizes machine performance, leveraging seasoned experience to anticipate problems before they escalate, keeping the automated feeding systems functional and efficient.
Support Feature | Function | Impact on Automated Feeders |
---|---|---|
Comprehensive Directory | Facilitates access to a wide range of technical expertise | Enables swift resolution of complex feeder challenges |
Sleep Mode Troubleshooting | Addresses issues causing unintended operational pauses | Prevents disruptions in continuous material flow |
Device Driver Management | Ensures all software interfaces with hardware components effectively | Maintains seamless communication between feeder parts and control systems |
Bluetooth Connectivity Support | Resolves issues with wireless interfaces and sensors | Upholds the integrity of remote monitoring and adjustments |
Training Staff on Basic Maintenance and Troubleshooting Procedures
In the domain of automated feeder management, it’s imperative for staff to receive training that encapsulates the nuances of environment variable adjustments, ensuring they are adept at maintaining the equilibrium necessary for optimal feeder operation. Equipping them with these skills allows for swift identification and rectification of issues, minimizing reliance on external support for minor malfunctions.
Training on resolution protocols that include interpreting feedback from the system’s URL or reconfiguring the connection to a printer is another critical element that staff must master. Proficiency in these areas supports a self-sufficient management team, capable of addressing a spectrum of troubleshooting scenarios that might otherwise halt production.
Frequently Asked Questions
What are the signs of common automated feeder issues?
Common automated feeder issues often manifest as irregular dispense patterns or complete failure to release feed. Another sign is unusual noises during operation, which can indicate a mechanical problem.
Which steps should I take first when troubleshooting a feeder?
When beginning to troubleshoot a feeder, start by checking for any obvious obstructions or debris that may be hindering its operation. Next, ensure that the feeder is receiving the correct power supply and that all electrical connections are secure and intact.
How do I handle mechanical failures in automated feeders?
When confronted with a mechanical failure in an automated feeder, the first step is to consult the device’s manual for troubleshooting guidelines. If these initial efforts fail to resolve the issue, seeking assistance from a professional technician who specializes in such equipment is advisable.
What’s the procedure for resolving electrical problems in feeders?
To address electrical issues in feeders, an electrician will typically begin by conducting a thorough diagnostic test to pinpoint the problem’s source. After identifying the fault, they will execute repairs or replace damaged components to restore proper function.
Can improved performance be expected after feeder optimization?
Optimizing a feeder can indeed lead to better performance, as it enhances the consistency and efficiency of material flow. This optimization usually results in reduced downtime and increased productivity.
Conclusion
Addressing automated feeder challenges sustains manufacturing efficiency by preempting interruptions and preserving the quality of output. Regular inspections and troubleshooting promote feeder longevity, while accurate diagnostics and timely repairs mitigate potential production setbacks. Preventative maintenance and staff training ensure feeders consistently perform their critical functions within operational standards. Ultimately, maintaining automated feeders through these strategies ensures uninterrupted production flow and the reliability of manufacturing processes.